For each of our more than 30 businesses, safety is a top priority. Because we tackle the big problems, we need processes that ensure the safety of our people and our environment. These are just two of the safety stories that happen at our locations every day, one close to home and one across the ocean.
Kallo’s Safety Milestone
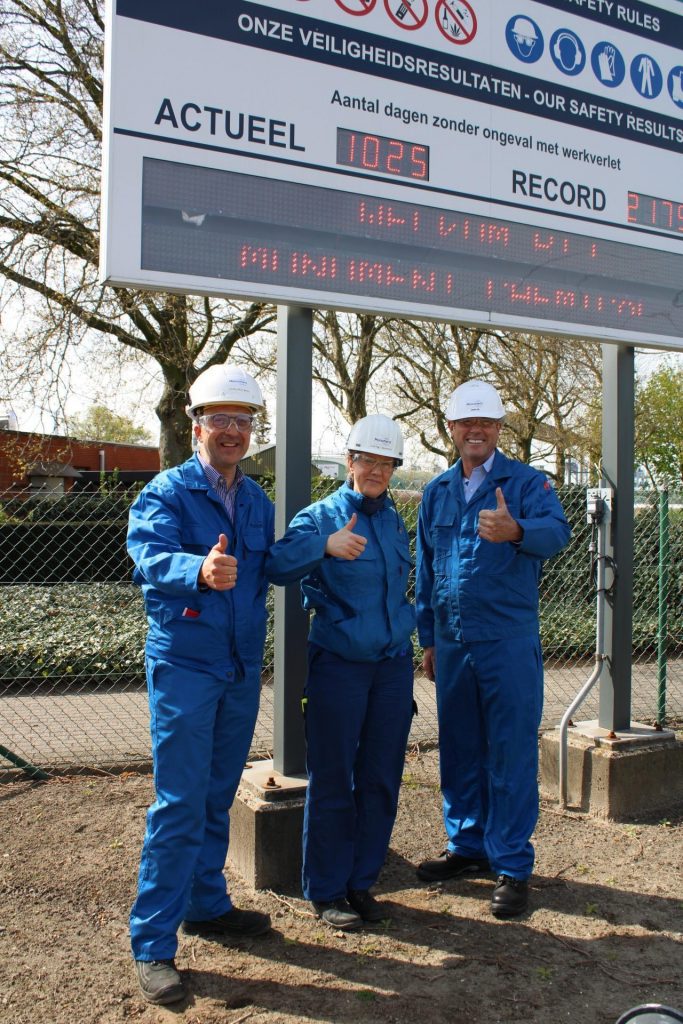
from left: Manu, Gretel and Monument CEO Paul Raymond celebrate the milestone on site.
On Thursday, March 17, 2022, Monument Chemical’s Kallo, Belgium, team hit 1000 days without a major safety incident or lost time injury. And with 130 employees and 70 contractors working on site at any given time, the focus on safety has a large net to cast.
“Safety is all about behavior, and repetition is how you change behavior,” Manu Gyselinck, Kallo site manager, explained. “So here at Kallo, the conversation never stops. We’re constantly reiterating the importance of reporting incidents, no matter how small. These ongoing discussions are designed to make people feel more comfortable speaking up. We want our team to understand that when you make something visible to everyone, it can become an opportunity to learn and improve.”
While it’s important that these efforts start from the top, teamwork is the only way they can actually be executed.
“When you’re talking about safety, you’re never alone,” Manu added. “We focus on tiered accountability. As a site manager, I have to push and pull these efforts forward through my own actions. But I always expect everyone on site to keep safety top of mind and motivate one another to share this mindset. Our teams know the impact these efforts have on themselves, their colleagues, and their families, so in this way, they become stakeholders in the process.”
Much of this success is due to the implementation of the “STOP Principle” that encourages putting safety first before production.
“If something is not going in the right direction, we have to stop and evaluate,” Manu shared. “Everyone has the right to raise their hand and stop the process to help keep things on track. In the end, it’s about taking care of the customer, our colleagues and the livelihood of the plant. And with a stronger plant, lower costs will follow.”
“With all the challenges on our plates each day, it’s easy to slip into a reactive mindset,” Adam Pingel, VP of operations, explained. “But that only makes it tougher to get in front of issues. Constantly reevaluating what we’re doing and how we can do it better can help us resolve issues more effectively and efficiently – and hopefully prevent them from ever happening in the first place.”
A week after the team reached the milestone, the site hosted a food truck serving a delicious lunch of hamburgers and french fries to everyone in the main office. It was a small way to show appreciation for the great effort from everyone on the team, and a reminder that safety isn’t just about hard work—when achieved together, it can also be fun.
“When we win in safety, there are great opportunities to celebrate,” Adam added. “And there are opportunities to do that every single day. Our milestone celebrations are great, but our real wins happen every day thanks to every single person on this team.”
Flying the Black Flag at AMI
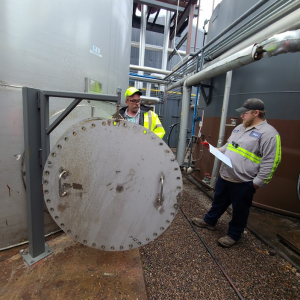
Hands-on confined space training at AMI’s Eau Claire, Wisconsin, location.
Stop-work authority is a policy that permits any employee to halt a job when they recognize a potentially hazardous or dangerous situation. At AMI, stop-work authority is called the Black Flag Safety Initiative — and it’s vital to maintaining a safe and empowering workplace culture.
If at any time an employee feels uncomfortable about a situation or task, they can stop and call “black flag.” This initiates a timeout that allows others to assess the potential for risk and put together a plan to address it, even if the risk seems small.
“Black flags can be as simple as an employee recognizing they need a different tool for a job or checking with a teammate if they’re getting too hot and need a break,” said Crystal Hudak, Regional Safety Director at AMI. “Many black flags are simply employees working hard, recognizing something isn’t right, and removing or mitigating the hazard as part of their everyday work.”
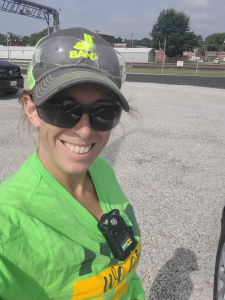
Crystal on the job in St. Elmo, Illinois.
A recent example of the black flag safety initiative comes from AMI’s Utica, Illinois, location. “An employee noticed that the amount of hot material a driver requested to load would put the total amount very close to the trailer’s maximum gallons,” Crystal said. “If there was an error in loading hot material, the trailer could have overflowed or material could have leaked out of the vent while the trailer was traveling down the road.” Recognizing the risk, the employee called black flag.
Ultimately, the driver and employee agreed to load less material, avoiding the potential for a leak. “This is a fantastic example of an employee noticing a potential safety or environmental issue and taking steps to address the hazard,” Crystal said.
Throwing the black flag – notifying your immediate supervisor of a hazard or concern – is everyone’s responsibility. Each employee is empowered with the same authority to stop work, meaning even AMI’s newest hires have the ability to ensure safety if an issue arises. “All employees are empowered to call a black flag, regardless of how many years they have on the job site,” Crystal said. “All of us can notice a hazard that someone else misses.”